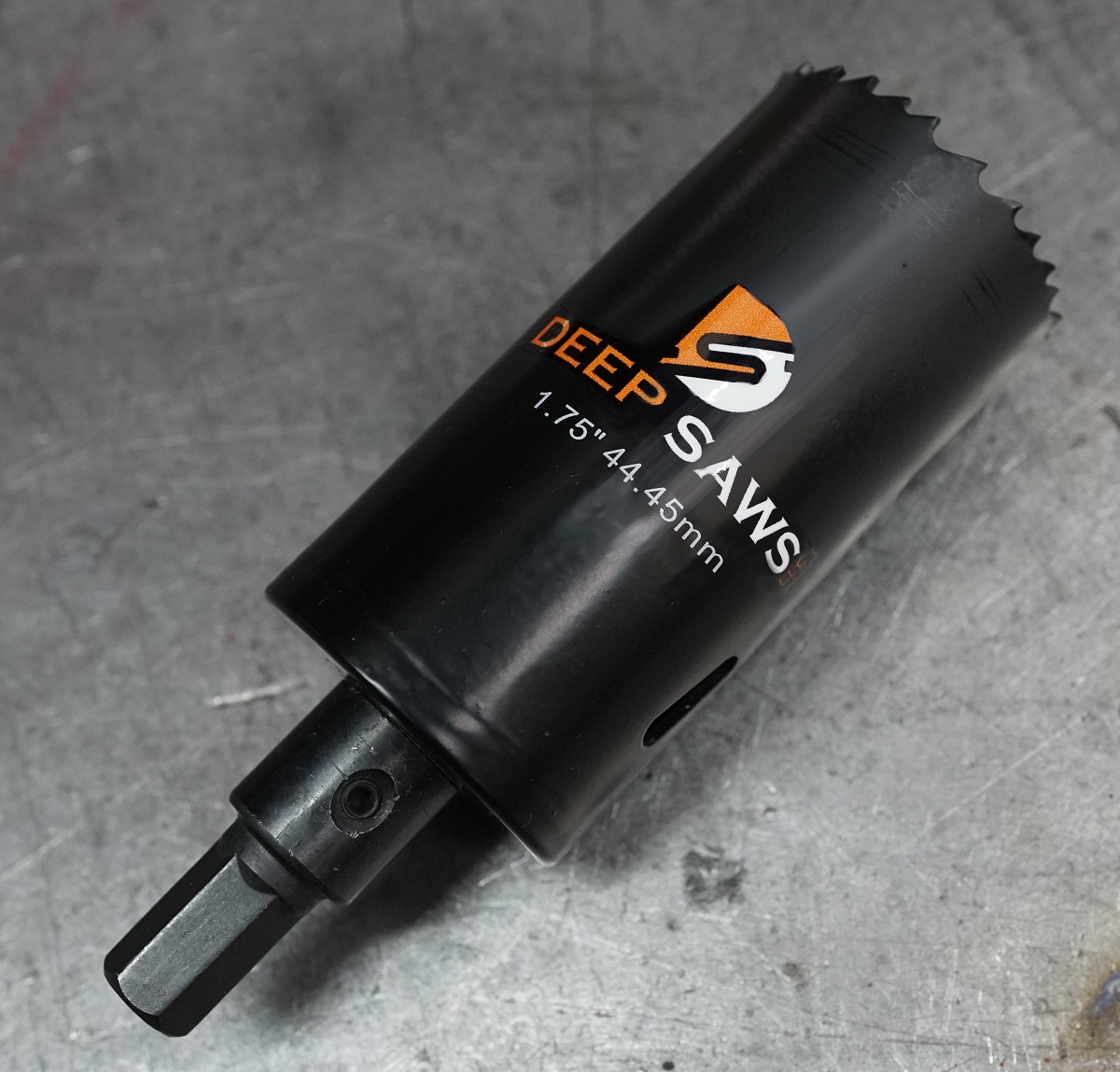
Choosing Which Hole Saw and How to Use It
WARNING: These are cutting tools. Always wear safety glasses. Be careful.
CAUTION: These hole saws are incredibly sharp and will dig into your material fast enough to stop themselves, your drill, and more. They must be used in accordance with these instructions to preserve their lifespan.
Cutting (VERY IMPORTANT)
Cutting oil – Unless you want to replace your hole saws frequently, use real cutting oil (like Tap Magic Pro Tap, which we sell). There are many cutting oils on the market, and WD-40, PB blaster, engine oil, and gear oil are extremely inferior to them.
Start with HIGH RPM and LIGHT FEED – Like other hole saws, these are a 4/6 variable pitch. There is over 1/8” between the teeth. Until you have cut deep enough that two or more teeth are engaging the material being cut, you must apply light cutting pressure at high RPM to prevent a single tooth from taking a super-deep cut and getting sheared off. If you tear teeth off your hole saws, it is from not doing this.
Leverage and arbor life—Using a hole saw with double the cutting length puts double the bending stress on your arbors. Steps 1 and 2 will help prevent your arbors from bending in regular use unless something goes wrong.
Warranty – While cutting consumables carry no warranty through our distributors, contact them if you have problems with these hole saws. We stand behind our products and want to know about your experience with them and have an opportunity to help if needed.
Fine Tooth vs. Coarse Tooth
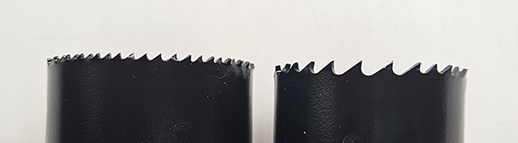
Fine Tooth: In general, is slower, has a smoother cut, grabs less with thinner material, clogs on aluminum
Coarse Tooth: Generally, it is faster, has a rough cut, grabs more with thinner material, and doesn’t clog up on aluminum.
If your material fits in the trough of the tooth, you should switch to a fine tooth.
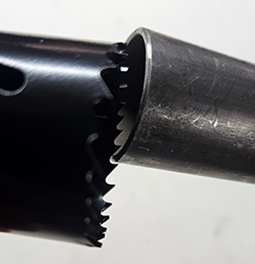
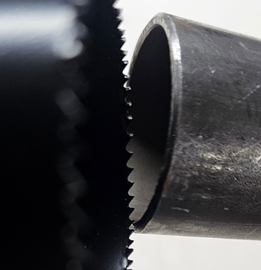
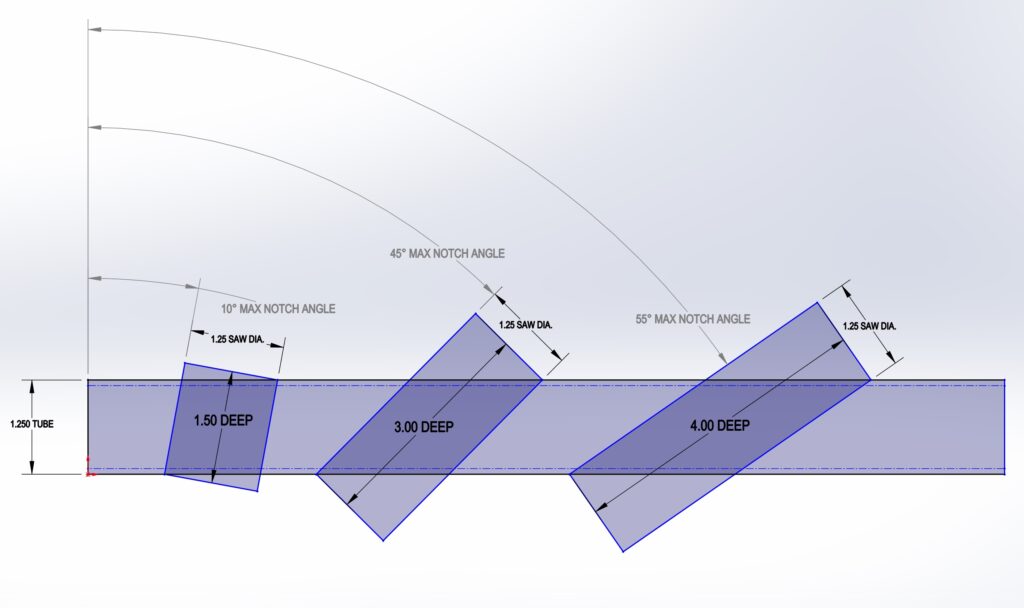
Cutting Tips:
Cutting Wood: Our deep-hole saws work like any other in wood.
Cutting Sheet Metal: You can drill through 1.5” thick wood to install a “slug” first to prevent the pilot bit from wandering when starting your cut. Once the hole saw is started, eject the slug and enjoy the full depth.
Notching Metal Tubing: This requires more finesse, and we have tips:
Deep hole saws chip load easier! Hole saws are “flimsy” by nature, and making them 3” or 4” long makes them flex more. We have done the R&D, watched them cut in 500+ FPS slow motion, and examined the flex, deflection, chip loading, and more. You WILL have to re-learn how to cut effectively to maximize tool life. That lesson will cost you a hole saw or two. Let us help you speed up the learning process:
From contact with tubing to .080″ depth of cut- run a corded 1/2″ chuck drill at 600-700 RPM. Wet the hole saw with TAP MAGIC or similar. NOT WD-40, engine oil, etc. Feed with about 1/2 pound force on the drill (very light feed force).
From the .080″ depth of cut to just before the end of the cut– run the drill at 300-700 RPM based on feel. We usually run on the high end of the RPM range and push with about 8-10 pounds of force. Re-apply some cutting fluid mid-cut one time.
End of cut- Max RPM and light feed again.
Remember that at the beginning of a cut, ONE tooth with an aggressive rake angle is cutting carbon steel (or another alloy) all by itself. This is a nasty job. Don’t ask the tool to cut .050″ per tooth! High RPM and light feed let it take the .005″-.010″ that it wants to on steel.
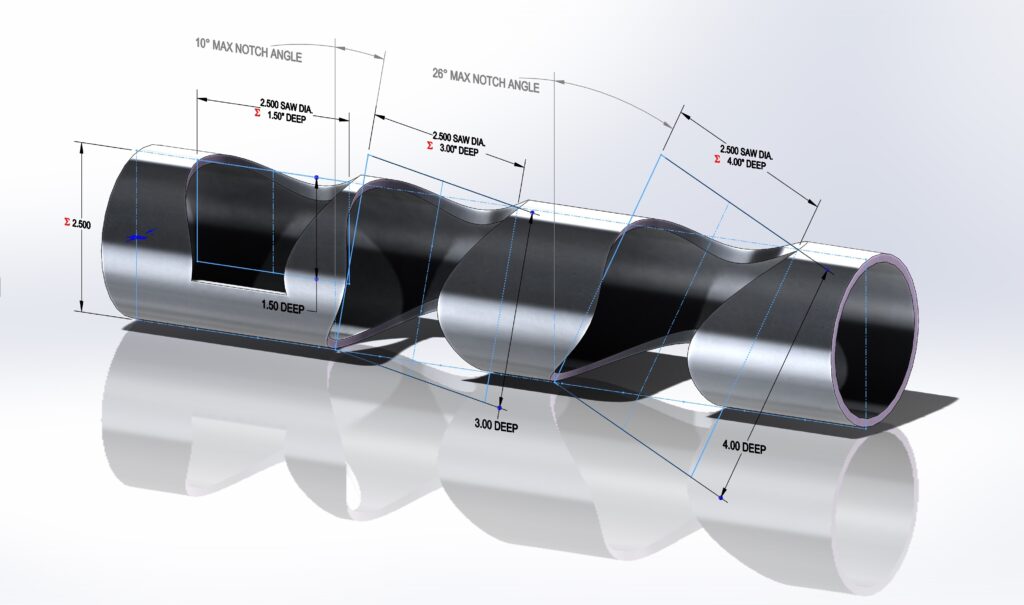
You can see above that this 2.50″ tube is notched with three different hole saws: 1.50″, 3.00″, and 4.00″ deep saws. The 1.50″ will need to do multiple cuts to get all the way through. The 3.00″ deep hole saw can get all the way through on the first cut with a 10-degree maximum notch angle. The 4.00″ deep hole saw can get all the way through on the first try as well, with a 26-degree maximum notch angle. We have visuals for this with 1.00″ tube, 1.25″ tube, 1.50″ tube, 1.625″ tube, and 2.00″ tube, with the corresponding degree changes.